Interface for CAD & CAM for DED based
Hybrid Manufacturing
Introduction


DED based 3D printed star at TAMU Smart Hybrid Machine Tool
Image Source: 3Diligent
The wide acceptance of the AM technology has extended beyond manufacturers to consumers. Manufacturing has been brought close to the consumers by allowing them to manufacture parts at the convenience of their homes. Such a development in manufacturing is being called as the maker revolution where the consumers get the power to manufacture their parts. To a great extent, this has allowed mass customization of products. However, these developments are still limited to 3D printing technologies like FDM.
​
The manufacturing ecosystem has now started to observe an open-source movement. Software that enables 3D printing is now available to all and their continual development by the open-source community ensures the improvement of the quality of the software. The RepRap project is an example of such an open-source development. There are many freely available software that exist today to design, slice and generate printing instructions to the FDM machines. However, metal-based additive manufacturing processes are still lacking in such open-source software and a supportive community that has been making FDM based printing accessible to a growing community.
​
This lack of attention is mostly because the metal-based additive manufacturing processes are not as well understood as are the polymer-based additive manufacturing processes. Metal-based AM technology is also more expensive than the commercial desktop 3D printers. Figure below shows our OPTOMEC HYBRID MACHINE which uses LENS technology to execute the additive manufacturing process chain.
​
​
​
​
​
​
​
​
​
​
Unlike an FDM based desktop printer, this machine occupies a large room. It is industrial grade with inlets for argon gas to drive the pneumatics. It consists of a chiller system for the safe operation of the laser while printing and a complex pathway for the delivery of the powder. The expensive machine along with its complexities has limited the DED process for applications in industries and research facilities. Therefore, unlike the open-source community for FDM printers, it has been difficult for DED based printing to attract members of such a community.
​
Besides all the complexities of the DED additive manufacturing that exist in operating the machine, the printing process planning itself in terms of part design and printing, although different are still very similar to the FDM printers. Figure below presents a typical sequence of steps that are involved between design conception and realization of a printed part. There exist software that handle the entire sequence of steps in the figure. for the FDM printers. CURA is an ideal example for such a case. But no such neatly packaged open-source software exist for DED printers, that is able to handle each of the steps. The machine has it’s own CNC instruction set in form of G-code and M-code to execute the printing process in the machine and therefore, the g-codes for the machine appear very different from the g-code for the FDM printers.
The additive manufacturing capability is only one part of a three-part story. Our machine is an OPTOMEC HYBRID MACHINE. The second part is the machining capabilities of the machine. In the hybrid machine, both additive and subtractive manufacturing process chains can be executed concurrently in the same cycle. Almost always, metal-based additive manufacturing processes require machining post-processing, due to the poor initial surface finish of the additively manufactured part, which requires the subsequent machining steps for improved surface finish. Such requirements exceed the capabilities of FDM software that are limited to only the printing step. We, therefore, tasked ourselves with developing an interface that generates codes for hybrid manufacturing, that is, instructions to the controller of the machine which consist of consecutive additive and subtractive manufacturing process chains within the same cycle.
​
The third part of the story is the augmentation of the OPTOMEC HYBRID MACHINE with sensors. The additive and subtractive manufacturing processes are its arms, limbs and its physical body. With the sensors, the machine also senses itself and has the potential to be self-correcting in its manufacturing capability. This extends the capability of hybrid manufacturing to smart manufacturing where the loop is closed and the machine is aware of itself. There is a wider aspect to our project and more details in this direction can be seen here.

OPTOMEC 3D HYBRID MACHINE TOOL

STEPS BETWEEN DESIGN CONCEPTION AND PRINTED PART
Highlights
Hybrid Manufacturing program generation
The interface generates G-codes for DED printing and subsequent Milling operations.
Open-source architecture written in Python
The interface was developed completely using open source packages in python allowing for modification and use among a broader community.
Challenges Addressed
-
Our interface is the first to bridge the gap between design and machine instruction. There existed no open-source software to generate G-codes for hybrid machining platforms with LENS based additive manufacturing process.
-
Process flow from design conception to manufacturing on the hybrid machine was streamlined with developed CAD/CAM interface providing the hybrid machine with quick prototyping capability.
-
Experimentation on the machine has been expedited by providing process parameter tuning capability on the interface itself.
-
What can be achieved with sequentially using existing software for FDM to generate the final machine instruction for the hybrid machine has been developed completely on an open-source platform. The program also binds 3D printing codes to even consequent machining codes in the same cycle.
-
Codes being generated with the correct offset for the laser head and the machine tool spindle head was critical to the safety of the machine since the laser head and machine tools share the same space in the machine.
The Interface
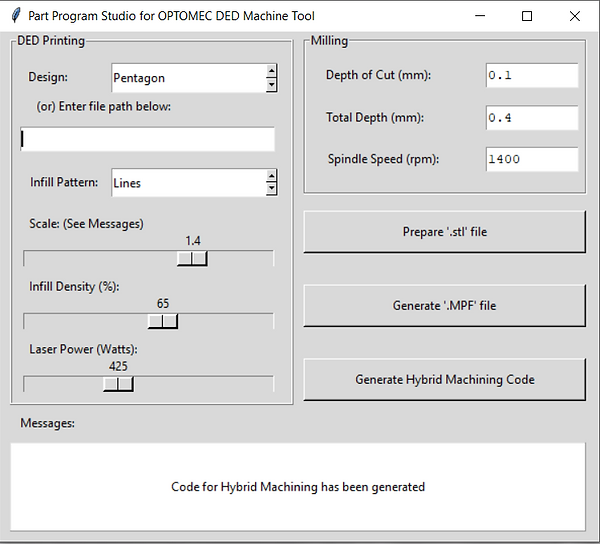
GUI DEVELOPED FOR GENERATING HYBRID MACHINING CODE
The graphical user interface enables the users to easily generate part programs for prismatic geometrical shapes or for custom downloaded or generated .stl files. The interface allows the user to scale the part according to the requirements of the print. The user can also select the printing process parameters such as infill pattern design, infill density and laser power. If required instructions for the milling operation on the printed part can also be generated from the interface. Through the interface users can finally generate a final part program file (.MPF format) with instructions to the machine for both DED printing and milling.
Using the Interface
​
VIDEO DEMONSTRATION ON USING THE INTERFACE
Limitations
-
It is still difficult to develop support structures to print complex parts. It may be possible to address this issue by modifying the codes to generate .stl files that include support structures. Also, delivery of support structure material is an important challenge to be addressed, since use of multiple powders from the same DED head will be a challenge.
-
It is challenging to print an object over another because of the inherent variation of the height of the printed part arising from the DED printing process itself.
-
While trying to print parts over other parts, it is important to be mindful of the dimensions of the bounding box of the layer being printed. Parts with subsequent layers of increasing bounding box dimensions will require addition of support structures must be designed and printed.
-
The optimal printing paths for the DED printing need to be calculated.
-
Distortions of the part during printing need to be factored in during the printing.
Hybrid Machine Printing
The star shaped prism that is being printed uses a part program that was generated using our interface.